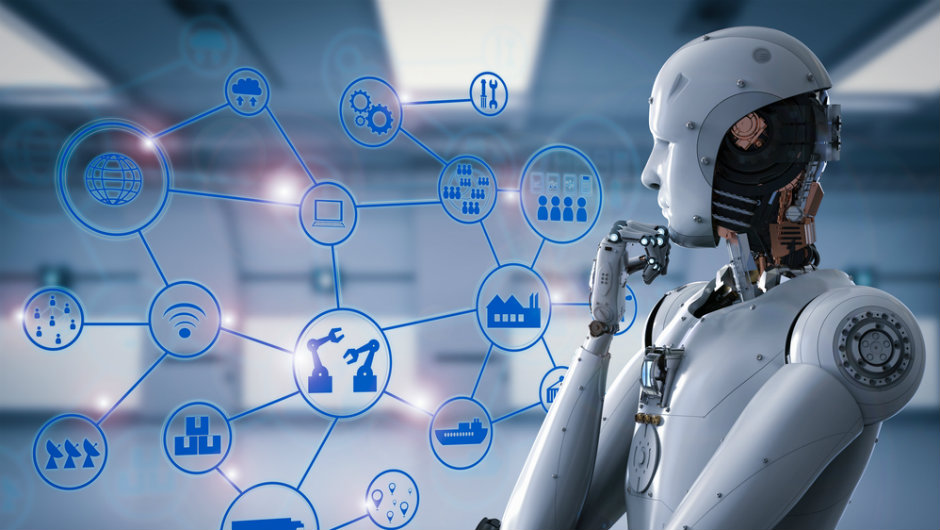
Son güncelleme: 23.08.2023
Diğer yazılarımızda robotun ne olduğuna, robot mekaniğine ve robot mekanizmasının ne şekilde oluşturulduğuna değindik. Bu kısımda ise işlevi yerine getiren mekanizmaları hareket ettirecek, istenilen fonksiyonu yerine getirmeyi sağlayacak olan bölümlere değineceğiz.
Robotun işlevine karar verip işlevi gerçekleştirecek mekanizmaları tasarladıktan sonra bu mekanizmayı hareket ettirecek olan sistemlerin oluşturulması gerekecektir. Bu sistemler tahrik sistemi olarak geçmekte olup ne şekilde yapıldığına göre isimlendirilmektedir. Diğer yazılarımızda değindiğimiz üzere ilk üretilen mekanizma ve makineler ısıl tahrik yani buhar gücü ile çalışmaktaydı. Buna benzer şekilde sıvı tahrik (hidrolik) hava tahriği (pnömatik) şekilde temel tahrik sistemleri yer almaktadır. Günümüzde ise robot teknolojisinde hız ve verim açısından bu tahrik sistemleri yerini elektrik tahriğine bırakmıştır. Hidrolik ve pnömatik tahrik sistemleri de bu hız ve verimin etkisinden faydalanmak için elektro-hidrolik ve elektro-pnömatik olacak şekilde güncellenmiştir. Ayrıca elektrik ve elektronik tahrik sistemleri, sensör ve mikrodenetleyiciler vasıtası ile esnek ve çok detaylı programlamaya yani kontrole sahiptir.
Öncelikle elektrik-elektronik kavramlarına ve elektrik tahrik ekipmanlarına değinelim. Sonrasında da robot üzerindeki uygulamalarına bahsederek ilerleyelim.
Hareket Tahrik Sistemleri
Elektrik, içine elektroniği de alan atomda yer alan elektron etkileri ile ortaya çıkan geniş bir enerji türüdür. Elektrik enerjisi manyetik cisimlerin de etkisi ile yönlendirilip neticesinde hareket enerjisi elde edilecek şekilde elektrik motoru olarak adlandırılan sistemlere dönüştürülmüştür. Elektrik, akım üzerinden doğru (DC) ve alternatif (AC) olmak üzere ikiye ayrılmıştır. Doğru akım ilk bulunan tip olup iletkenin iki ucu arasında elektriksel potansiyel farkın (volt) geçişi şeklinde ortaya çıkmıştır. Manyetik etki ile ortaya çıkan elektrik akımı ise alternatif akım olarak adlandırılmaktadır. Elektrik enerjisinin kontrol edilmesi fikri ile de elektronik bilgisi ortaya çıkmıştır. Elektronik, Elektrik enerjisinin genel olarak DC, yani doğru akım yönüyle ilgilenmekte olup yarı iletken elementler (silisyum, germanyum, galyum gibi) ile bu enerjinin depolanmasını, iletilmesini tetiklenmesini sağlayarak elektrik enerjisi üzerine kontrol ortaya çıkarmıştır. Günümüzde elektrik enerjisi temel olarak, AC biçimde yaşam alanlarına gelmektedir. Kullandığımız cihazlarda AC akım DC’ye dönüşüp elektronik devreler vasıtası ile ilgili işlevlerini yerine getirmektedir.
Elektrik ve elektronik kavramlarından hareketle robot için hareketi sağlayacak elektrik tahrik sistemlerine göz atalım.
Elektrik tahriğinin en temel ve en yaygın unsuru elektrik motorlarıdır. Elektrik’in sınıflandırıldığı gibi motorlar da AC ve DC olarak ayrılıp içlerindeki durağan manyetik yapı (stator) ve hareket eden manyetik yapı (rotor) tiplerine göre sınıflandırılır. Sınıflandırma, dallara ayrılarak stator rotorun dizilimine göre ayrılır. Mekanik yapıya göre de farklı hareket ve mekanizma sağlayacak şekilde sınıflandırılmaktadır. Endüstriyel robotlarda ve CNC tezgahlarda yaygın olarak AC ve DC tipte, kaldıracağı yüke göre farklı güç mertebelerinde Servo Motorlar kullanılmaktadır.
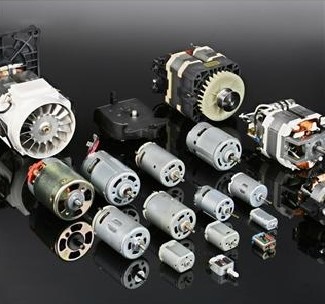
Elektrik motorlarından sonra endüstride en çok kullanılan ve yaygın olan sistem elektro-pnömatik sistemlerdir. Endüstriyel robotlarda en çok gripper (tutucu) mekanizmalarında kullanılmaktadır. Bu sistemler hava tahriğine (pnömatik) elektriksel kontrol neticesinde ortaya çıkmış temiz, kullanışlı, kontrolü kolay ve esnek düzenleme sağlayan sistemlerdir.
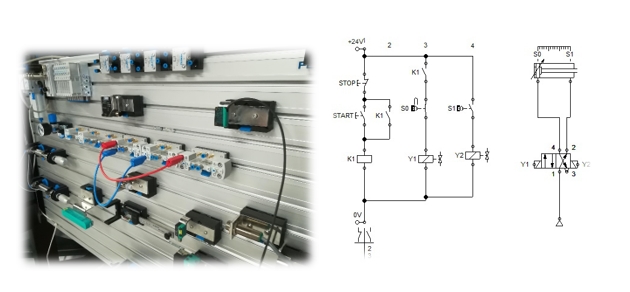
Yine akışkan temelli olup pnömatiğe benzer sisteme sahip olan hirolik tahriğe (sıvı) elektrik kontrolü eklenmesi ile oluşan sistemlere elektro-hidrolik sistemler denilmektedir. Elektro-pnömatik sistemlerde havanın sıkışma, basınç ve kuvveti sıvıya göre düşük olmasından ötürü yüksek güç gereken yerlerde elektro-hidrolik tahrikler kullanılmaktadır.

Tahrik Kontrol Sistemleri
Tahrik sistemlerini genel olarak inceledik bu sistemleri de kontrol etmek için çevresel bileşenler üzerinden bir geri bildirim (feed back) almak için algılayıcılara ihtiyaç duyulmaktadır. Bu algılayacılar, günümüzde tahrik ve kontrol sistemlerine uyumu için elektrik tabanlı olan sensörlerdir. Dünya, etkiler ve büyüklükler olarak elektrik anlamında analog ve dijital olarak ikiye ayrılmaktadır. Isı, ışık, ses, gaz, mesafe vb. gibi fiziksel büyüklükler analog büyüklük olarak adlandırılırken, elektriksel büyüklükler 1 ve 0 (var-yok) olarak nitelendirilen iki çeşit sinyalden oluşup dijital (sayısal) olarak adlandırılmaktadır. Sensörler, fiziksel sistemler (analog) ve elektrik sistemler (dijital) arasında köprü kurar. Özetle sensörler fiziksel etkileri elektrik sinyaline (1-0) dönüştürerek mikrodenetleyicilere bilgi üretir.
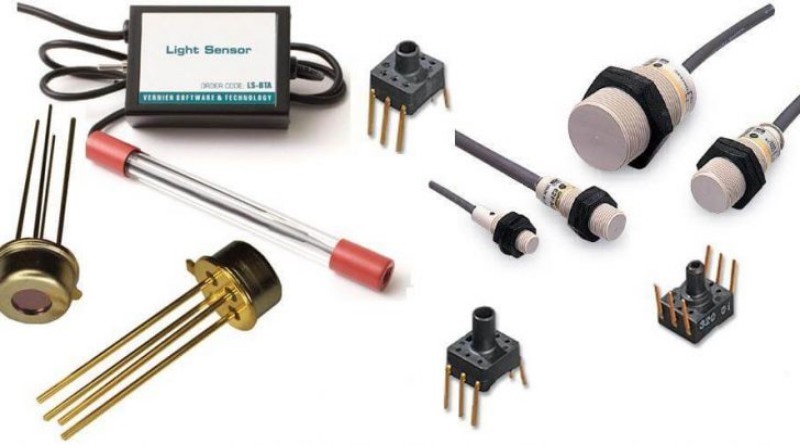
Tahrik sistemleri için geri bildirim ve bilgi sisteminin sensörler ile kurulmasıyla birlikte bu tahrik sistemlerini kontol için gerekli olan kontrolörlerden bahsedelim. Bu kontrolcüler yine elektrik ve elektronik sistemlerden oluşmakta olup sensör ve mikrodenetleyiciler ile uyumlu olarak sistem hareketini sağlamaktadır. Örnek olarak, bir elektrik motoruna enerji verildiğinde motor mili tek bir yöne devamlı olarak belirli bir hız ve kuvvette dönme hareketi yapacaktır. Motora belirli hız, konum ve güç gibi değerleri verecek elektrik-elektronik tabanlı sistemlere “Sürücü (Driver)” ismi verilmektedir. Aynı şekilde pnömatik bir pistonu ileri-geri olarak hareket ettirecek, belirli hız ve konumu sağlayacak olan elektro-pnömatik valf veya bobin sistemleri bulunmaktadır. Sürücüler, valfler, bobinler,röleler ve kontaktörler vb. sistemler tahrik sistemlerinin yapılarına göre farklılık gösterip farklı isimlerde anılan kontrolcü sistemlerdir. Bu sistemler, programlamayı sağlayan ve ana kontrolcü olan mikrodenetleyiciler ve kontrolörler ile tahrik sistemleri arasında düzenlemeyi sağlayan ara kontrolcülerdir. Bu kontrolcü sistemlerin fonksiyonelliği ve kontrol ağı arttıkça mikrodenetleyiciye yani ana kontrolcüye binen yük ve programlama işleri o denli azalacaktır. Aşağıda bu sistemlerin örnekleri yer almaktadır.
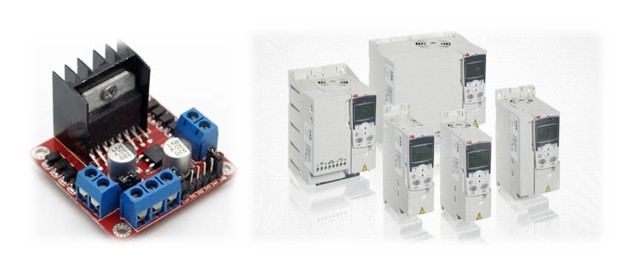
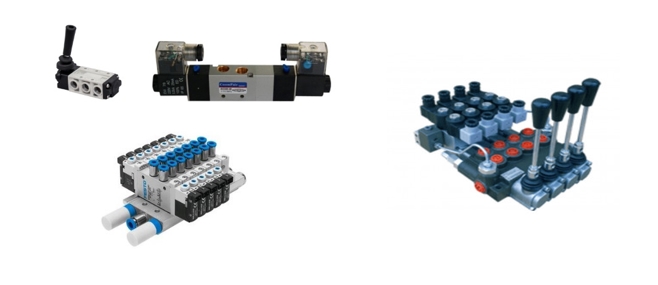
Robot Genel Yapısı
Diğer yazılarımızda bahsetmiş olduğumuz 6 serbestlik dereceli endüstriyel robotun hareket ve kontrol sistemleri aşağıda özet şeklinde gösterilmiştir.
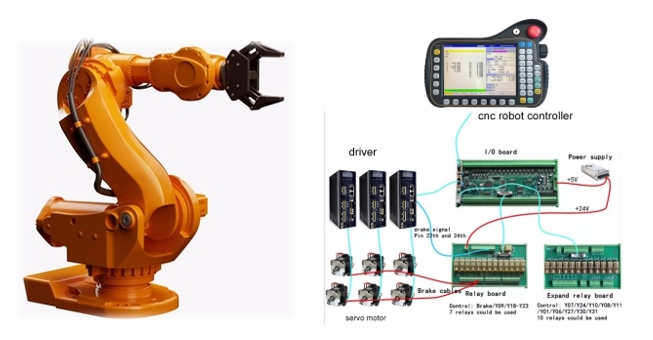
Tıpkı endüstriyel robotun sahip olduğu sisteme benzer yapıyı tüm robotlarda görebilmek mümkündür. Diğer yazılarımızda bahsetmiş olduğumuz işlevine göre sınıflandırılan robotların basit bir örneği olan ışık izleyen robotun yapısını ve onu oluşturan elektronik devreyi aşağıda görebilirsiniz. Işık izleyen robotun çalışma prensibi oldukça basittir. Bu nedenle mikroişlemciye yani programlamaya ihtiyaç duymadan sensör, elektronik devre elemanları ve motor bileşenleri ile robot oluşturulabilmktedir. Işığa duyarlı olarak artıp azalan dirence sahip olan LDR sensörünün direnci arttıkça veya azaldıkça motoru tektikleyecek olan elektronik devre elemanı transistör üzerinden akım geçer akım geçtikçe transistör tetiklenir ve motora enerji gider ve motor harekete geçerek robot çalışır. LDR ve motor devresi iki adet yapılarak robotun iki motor ile sağa ve sola gidişi de bu söz konusu iki motorun ucuna takılacak tekerlekler ve önünde her yöne gidebilecek avare tekerlek ile sağlanmış olur.
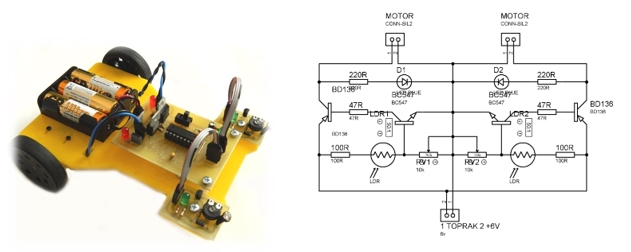
Görüldüğü üzere daha üst sisteme sahip olan robot ile basit yapılı robot arasında farklılıklar bulunsa da temelde aynı sistemlerden oluşurlar. Endüstriyel robotlarda motor gücü ve ebatları büyüdükçe onu kontrol eden sürücü de karmaşıklaşır, ışık izleyen robotta ise motor DC ve az akım ile çalışır ve sadece elektrik akımının transistör üzerinden gelmesi ile harekete geçer. Sensör olarak endüstriyel robotta mesafe algılayan endüstriyel şartlara dayanıklı kapasitif sensör bulunurken ışık izleyen robotta motora hangi şartta harekete geçeceğini bildiren ışığa duyarlı LDR sensör yer almaktadır. Endüstriyel robotun işlev ve fonksiyonu çok olup çok amaçlı kullanılabileceğinden ayrıca mikroişlemci ve denetleyiciler ile programlanması gerekir. Ancak ışık izleyen robot işlevini sensör etkisi ile gerçekleştirdiğinden programlama ihtiyacı oluşmamıştır.
Mikrodenetleyiciler ve Programlama
Tüm bu mekanik, elektrik-elektronik sistemi kontrol etmeyi sağlayan vücudumuzda beyin olarak tanımlanabilecek, tahrik, sensör, ara kontrolcü sistemlerini düzenleyen ve programların yazıldığı mikrodenetleyicilerden bahsedelim. İçerisinde bir CPU (Central Processing Unit/Merkezi İşlem Birimi), ön bellek ve input/output (giriş/çıkış) birimleri bulunan elektronik devreler mikroişlemci olarak adlandırılmaktadır. Mikroişlemciler, bulundukları elektronik yapıların ana kontrolcüleridir. Bağlı oldukları sistemlerin denetleme ve düzenlenmesini sağlarlar. Mikrodenetleyici ise dışarıdan gelen bir veriyi (programı) hafızasına alan, derleyen ve sonucunda da çıktı elde eden bir kontrolcüdür. Mikrodenetleyicinin yapısında: CPU, RAM, ROM, I/O Portları, Seri ve Paralel Portlar, Sayıcılar, Zamanlayıcılar, bazı tiplerinde de A/D (Analog to Digital) ve D/A (Digital to Analog) çeviriciler bulunur.
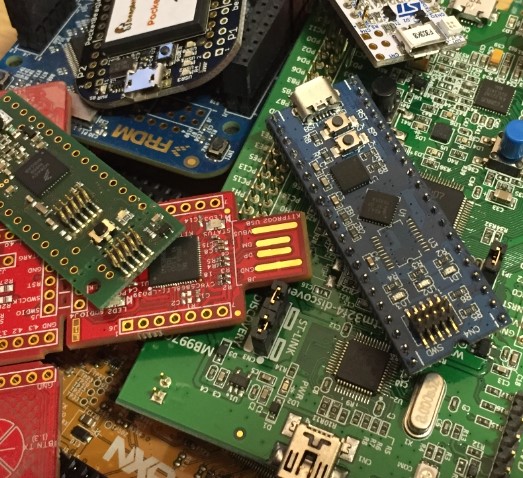
Mikroişlemci ile mikrodenetleyici birbirine karıştırılmamalıdır. Mikrodenetleyiciler, yapılarında mikroişlemcileri de içermektedir. Mikroişlemcilerin yapısında CPU, ön bellek ve I/O portları olmasına karşın mikrodenetleyicilerde ayrıca seri ve paralel portlar, sayıcılar, zamanlayıcılar ve çeviriciler (converter) de bulunmaktadır. Mikrodenetleyiciler, gerçek zamanlı uygulamalarda daha başarılı çalışmaktadırlar. Mikrodenetleyiciler bir işlevi çok küçük boyutlarda ve daha az enerji harcayarak yapabilmektedirler. Bunun yanı sıra mikroişlemciler aynı anda çoklu işlem yapabilirken mikrodenetleyiciler aynı anda tek bir iş yapabilmektedir.
Robotlar gibi elektriksel sistemlerin denetleme ve programlanması mikrodenetleyiciler ile gerçekleşmektedir. Mikrodenetleyicilerin endüstriyel olan seviyesi programlanabilir mantıksal kontrolör olarak adlandırılan, İngilizce (PLC) Programmable Logic Controller şeklinde isimlendirilen PLC’lerdir. Endüstri şartlarında sistemlerin kontrol ve denetimini gerçekleştirir. Temeli, yapısı ve işlevi aynı olmakla birlikte enerji düzeyi bakımından daha yüksek voltaj değerleri ile çalışması ile farklılık göstermektedir.
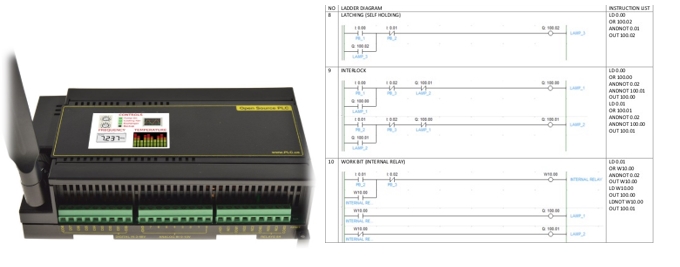
Mikrodenetleyici ve PLC’ler, elektrik-elektronik sistemlerden gelen 1 ve 0 sinyallerini işleyip, karşılaştırıp belirli bir fonksiyonu yerine getirmek üzere yine bu sistemlere çıkış üreten programlamanın yapıldığı elektronik yapılardır. PLC ve mikrodenetleyicilerin kendi içinde veya dışında bilgisayar ile bağlantı sağlayan derleyici ara birimi ve bilgisayar içinde program yazılmasını sağlayan yazılımları bulunur. İlgili yazılım bilgisayar ortamında yazılarak derleyici vasıtası ile ilgili PLC veya mikrodenetleyiciye aktarılır. Burada program içinde diğer elektrik-elektronik bileşenlerden gelen sinyaller program içinde giriş olarak tanımlanıp çeşitli karar, döngü, karşılaştırma, sayma ve zamanlama vb. işlemleri yapılarak netice olarak yine 1 ve 0 şeklinde çıkış sinyali giriş alınan bileşenlere aktarılarak kontrol sağlanmış olur.
Mikrodenetleyici, PLC ve Robot Kontrolörü vb. ile yazılan programlar, masaüstü yazılım uygulamaları ile karıştırılmamalıdır. Buradaki programlama işlemi çevresel birimleri kontrol etmek ve alınan dijital sinyalleri işleyerek denetleme ve düzenleme oluşturarak bir işlevi yerine getirme güdülmektedir. Özetle bu işleme makine programlama denilebilir.
FRC Robotu Elektrik-Elektronik ve Tahrik Sistemi
FRC yarışması için yapılan robotun elektrik-elektronik ve programlamasına değinerek yazımızı tamamlayalım.
FRC için hazırlanan robotta hareket işlemleri 12 V DC redüktörlü ve redüktörsüz motorlar ile sağlanmıştır. Motor kontrolleri spark ve talon motor sürücüler ile sağlanmıştır. Talon sürücüler kendi içinde mikrodenetleyici ve CAN hattı ile haberleşme sağlayarak 1-0 sinyali ile işlem yapmaya ihtiyaç duymamıştır. Sensör olarak lift mekanizmasının duracağı maksimum ve minimum limitlerin belirlenmesi için End-Stop anahtarları kullanılmıştır. Ayrıca robot kontrolü wi-fi ağı ile uzaktan kontrol şeklinde sağlanmıştır. Ağ bağlantısı sağlayan robot radio adlı cihaz ile sistemin tüm elektrik-elektronik bileşenlerini bir araya getiren dağıtıcı birim kullanılmıştır. Sistemin tüm güç gereksinimi 12 V güç kaynağı olan akü ile sağlanmıştır. Tüm bileşenleri kontrol eden mikrodeneteleyici olarak RoboRio kullanılmış olup programlama ve derleme işlemleri LabView programı üzerinden fonksiyon blokları ile yapılmıştır. Aşağıda SOLIDWORKS üzerinde tasarlanan robot mekanik sistemi üzerine yine SOLIDWORKS’te oluşturulan elektrik-elektronik bileşenlerin tasarımları montaj şeklinde yer almaktadır.
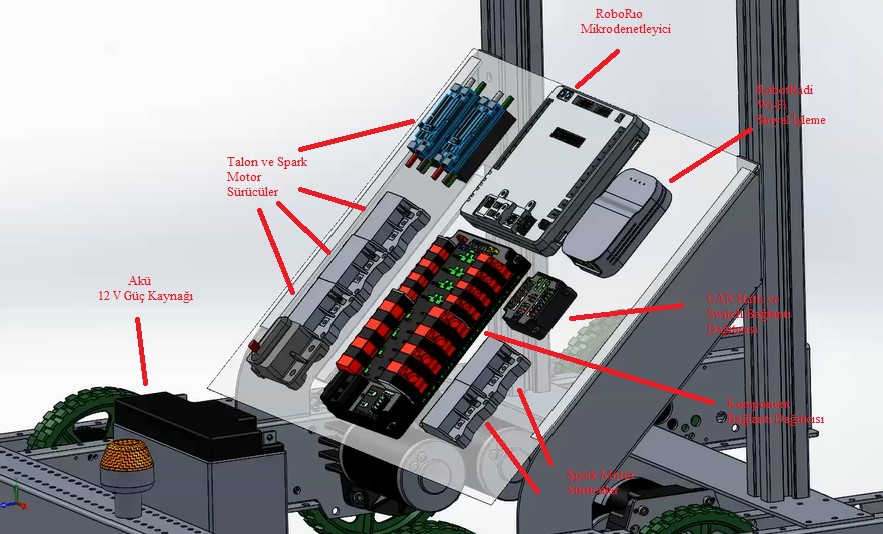
FRC robotunda ileri-geri ve sağ-sol hareketlerini sağlayacak olan tekerlekler için yukarıdaki resimde de görüldüğü gibi karşılıklı 2 şer tane olmak üzere 4 adet 12 V DC Motor kullanıldı. Motorlar kendi içinde ikişerli olarak senkronize diğer ikisi ile tersinir hareket etmektedir. 4 adet motor için 4 adet spark motor sürücü kullanıldı.
Bu motorlar diğer tüm sistem gibi uzaktan bir joystick ile kontrol edileceğinden aynı şekilde RoboRio mikrodenetleyicisi ile bağlantısı sağlandı. Güç ve motor bağlantılarının yanı sıra RoboRio ile sinyali Wi-Fi ile gönderen Robotradio bağlantısı gerçekleştirildi.
Lift mekanizması için yine kuvvet etkisini arttırmak için 1 adet 12 V DC Redüktörlü Motor kullanıldı. Bu motorun kontrolü için yine spark motor sürücü ile ve uzaktan erişim sağlanacağı için RoboRio ile bağlantıları sağlandı. Ek olarak lift mekanizmasını durduracak End-Stop (Limit Switch) sensör verisi spark motor sürücüsüne bağlandı End-Stop sensörüne bilgi gittiğinde bu sinyal ile motor sürücü enerjisi kesilerek motor durmaktadır.
Gripper kontrolü için ise yine 4 adet bu defa gücü diğerlerinden düşük ve küçük ebatlı DC motor kullanıldı. Bu motorlar, kutunun gripper içine çekilmesi ve atılması için tekerlekleri hareket ettirmek için kullanıldı. Motorlar bu kısımda ilgili çekme ve atma işlemini sağlaması amacıyla tersinir dönme hareketini gerçekleştirdi. Bu motorlar için güç bağlantıları birbirlerine göre ters bağlandı. Bu 4 adet motorun kontrollerinde ise birbirlerine CAN hattı ile haberleşmesi olan 2 adet talon sürücü kullanıldı. Talon sürücülerin güç aktarma oranı yüksek olduğundan bu kısım için bu sürücü tercih edildi.
İlgili komponentlerin bağlantı şemaları ve 3 boyutlu olarak kablo tasarımı SOLIDWORKS Electrical ve SOLIDWORK Electrical 3D ile sağlandı aşağıda bu şekilde oluşturulan tasarımı ve Robot Devresini inceleyebilirsiniz.
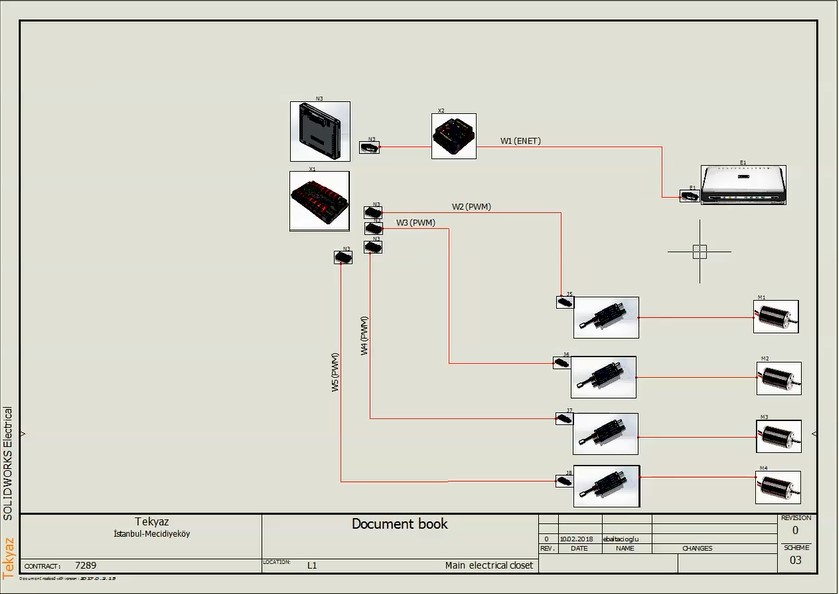
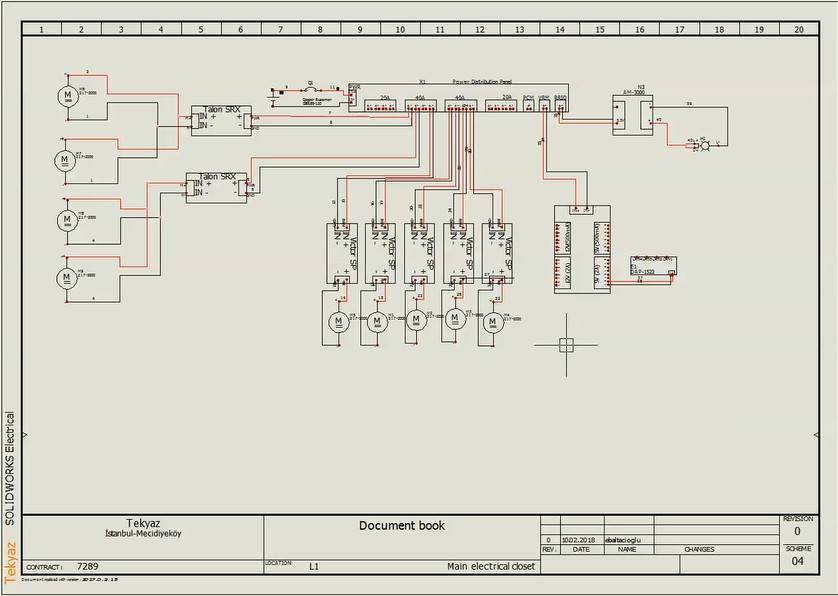
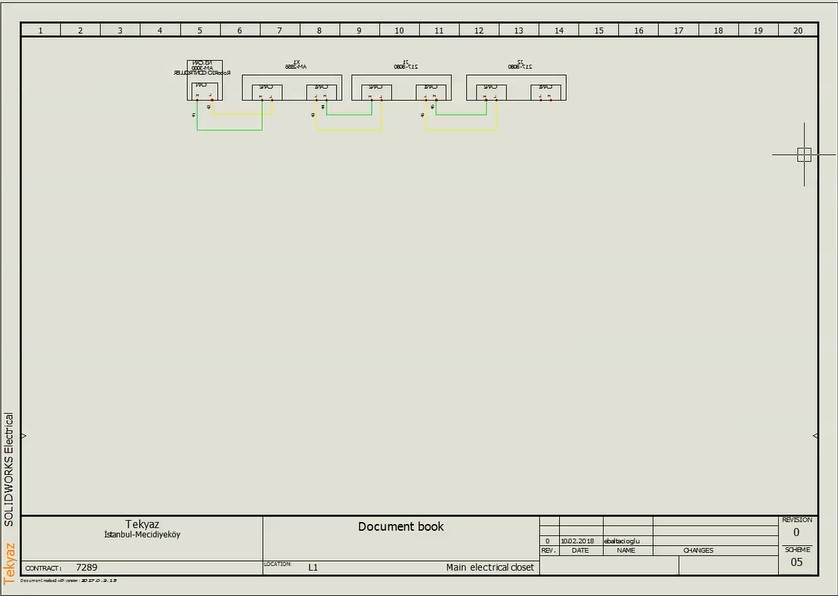
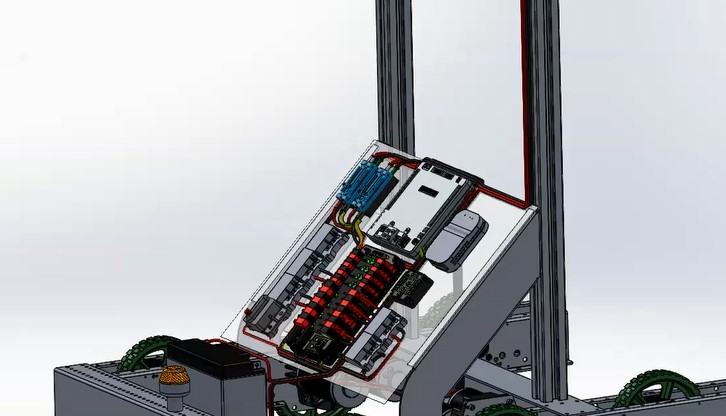
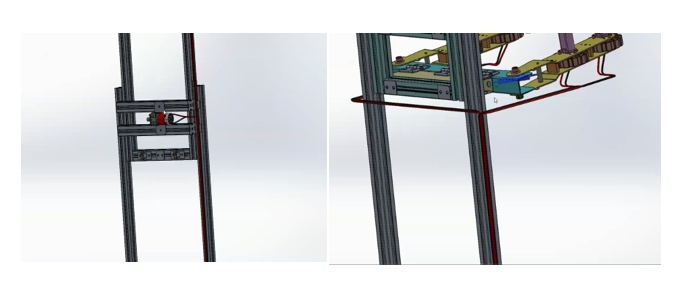
SOLIDWORKS Electrical 3D ile robotun oluşturulan devresinin 3 boyutlu tasarımda ne şekilde olacağını öngörmek oldukça yararlı. Robotun elektrik devresi ve kablolaması ile ilgili “FRC 2018 Yarışmasında SOLIDWORKS Electrical Uygulaması” isimli makalemizden detaylı olarak bilgi edinebilirsiniz.
FRC Robotu Programlama
Son aşama olarak FRC için yapılan robotun LabView programı üzerinden programlanması konusuna değineceğiz. Bu kısımda tüm program uzun olacağı için sadece bize temel olan programdan bahsedeceğiz. İlgili program, uzaktan kontrol ile joystick üzerinde bir tuşa bastığımızda motorun istenilen yönde, istenilen hızda hareket etmesidir. Bu durum için aşağıda FRC’nin kendi sitesinde yer alan temel motor kontrol programını kullanarak işlem yaptık. Tüm robot boyunca bu programın varyasyon, çeşitlendirmesi kullanılmış olup motor sayısına göre arttırılma yapılarak program oluşturulmuştur. Burada LabView üzerinden programlama yapılırken öncelikle başlangıç kısmı (Begin) olarak tuş tanımlama ve motor blokları kullanılır daha sonra ana kısımda (Main) motor bloğu üzerinden ilgili tuş sinyali alınıp karşılaştırılarak motor set bloğu oluşturulup çıkış üretilir. Aşağıda örnek program yer almaktadır.
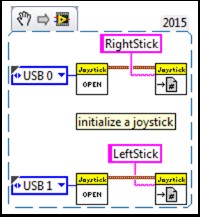
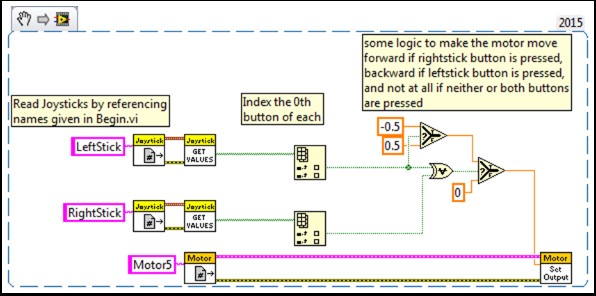
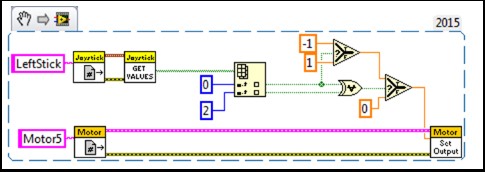
Bu program yazımı ve örneklerini FRC’nin kendi resmi sitesinde bulabilirsiniz. Buradaki örnekleri temel alarak kendi program varyasyonlarınızı oluşturabilir kontrol senaryonuzu belirleyebilirsiniz.
FRC Robot Programlama Örnekleri
Bir Önceki Konu
Robot Nasıl Yapılır – 3 – Mekanik ve FRC